
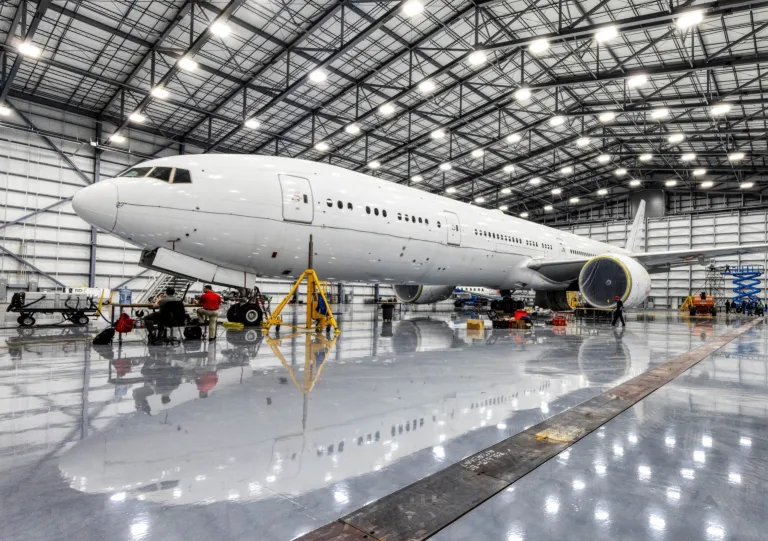
From the Cockpit with KMC’s Gibbs and NIAR’s Kivett
KMC president and NIAR program manager on the 777-300ERCF conversion
With three different 777 conversion programs currently in development, the large-widebody segment now offers plenty of choice.
The public-private partnership involving Wichita State University’s National Institute for Aviation Research (NIAR) and Kansas Modification Center (KMC) announced its 777-300ER conversion project in late September 2020 and received the prototype aircraft (37704, ex-Emirates) at its facility in Wichita (IAB) in September 2021.
Cargo Facts caught up with Jim Gibbs, president and CEO of KMC, and Eric Kivett, 777-300ERCF program manager at NIAR WERX, to discuss the 777-300ERCF program, which recently completed ground-vibration testing on unit 37704.
Cargo Facts: What’s the status of your 777-300ER conversion program?
Eric Kivett: Right now, we are in preliminary design. A key milestone that we passed was the submission of the project-specific certification plan that occurred back in January, right on schedule. Actually, the petitions for exemptions were published and the comment period has ended, so we’re awaiting feedback if there are any comments on our exemptions requests. We’ll be doing detailed designs through the second quarter of 2023, and then modification of the first aircraft in the second half of 2023.
We’ll be doing testing starting the end of 2023 and the first quarter of 2024, with planned STC approval in the second quarter of 2024. We’re proceeding well with the application package and ongoing communications with the Federal Aviation Administration (FAA). We’ve worked very hard to establish a positive relationship with them.
CF: How has the demand for 777 conversions evolved in the past two years?
Jim Gibbs: I’ll never forget the week that we launched, when oil was negative. Oil has been $150 a barrel since then. But with the advent of everything from COVID to the Ukraine crisis and others around the world, the demand has stayed pretty strong and pretty level with the amount of marketing that we have. You put a certain amount of marketing resources in and you have a certain amount of return. As we increase marketing resources, we expect higher returns and higher numbers on that end.
So it’s been really accepted much better than we ever possibly could imagine and it has not really had a lot of highs and lows in that respect. That has mirrored what we’ve seen throughout the world in the last few years.
CF: Your 777 conversion features a forward cargo door. What factors were behind this?
JG: The reason we’ve chosen the forward location specifically for weight efficiency on the fuselage. The 777 aircraft has a huge empennage and is a huge twinjet. If one of the engines were to go down and you suffered an engine-out scenario, the aircraft especially from the wing to the tail section would experience such heavy stresses that in order to get a big 10-foot-by-12-foot hole in it, you would need reinforcements around the entire circumference of the airplane.
When we look at the door’s location, about the only really good argument that we can find for having a rear door is commonality with the production 777F. The production freighter is shorter so there’s really not a lot of room to put it in front of the wing unless you get into the non-constant section of the fuselage, which is really not a very wise idea. We feel that our design lends itself to ease of loading of the aircraft and a lighter aircraft to begin with.
CF: Tell us about your conversion facilities in Wichita.
EK: Everything is essentially co-located in Wichita and within fifteen minutes of each other. So if there’s something with the airplane that the engineers need to look at, they’re five minutes away from it; it’s not a call to a different time zone, more emails and pictures to try to sort out what’s going on. The mechanic can see firsthand what the question is.
The first aircraft is split between the Air Force One hangar, which is the old hangar, and the new 75,000-square-foot hangar that opened in January 2022. There’s still a lot of room in that hangar, but we’ve already broken ground on the next new hangar just south of it. Both of these will be dedicated fully to 777 conversions and we also have plans for more hangars in the future that will start here pretty soon.
CF: Do you foresee all future expansions being on site? Or do you anticipate working with other MRO partners elsewhere, either in or outside the country?
JG: We’ve been asked if we’d be interested in that. I would say that until we get the first ten to twelve aircraft completed and feel confident in the process, and if there would be a team member that could prove their quality and delivery capabilities to us, it’s something that we would study. But at this moment, we haven’t found an example yet that we would like to use. It’s not that there isn’t somebody out there, but in order for us to do something like that, we would have to severely vet their quality, delivery and business aspects of it.
CF: What kinds of setbacks have you experienced and learned from so far?
JG: This is probably the most emotional business that you’ll ever be attached to. We have daily battles; we have daily setbacks; we gain and we analyze risk, day by day, month by month. Our schedule is aggressive but it’s realistic, and one aspect of having a realistic schedule is to have some buffer in there for items that are not anticipated. So do we have setbacks? Absolutely we have setbacks. But as the setbacks come up, we look, we plan and we mitigate the risk of each and every setback that we have.
EK: I think probably the biggest technical challenge is still ahead of us. We don’t know what it is yet. We’ve had some technical challenges, but I wouldn’t consider them setbacks. I’ve been in the industry thirty-five years, and I’ve seen much more significant technical challenges than what we’ve encountered to date. I’d almost say that what we’ve encountered so far is normal in the aerospace industry. We will hit some challenges, but we have a very talented team capable of sitting down, assessing the facts and identifying the possible next courses of action to go about solving the problem.